Question 1: List and describe four different kinds of layouts for a factory.
Question 2: Two machining operations, A (3 minutes per part) and B (10 minutes per part), are performed sequentially to manufacture a part. Machines A and B produce 5% and 6% defective items, correspondingly. The factory operates 8 hours each day, 5 days per week, and 4.2 weeks per month. Every day each machine requires 0.30 hour for being set up. Find the machine fraction for each type (A and B) if we require to handle a demand of 1000 items per month. Use a machine-up factor equal to 85% for each machine.

Question 3: A manufacturing facility comprises of five departments 1, 2, 3, 4 and 5. It produces four components having the manufacturing product routings and production volumes indicated in the table below.
a) Generate a from-to chart.
b) Find a relationship chart by using the given rules: “A” for 85-66 trips between departments, “E” for 65-46, “I” for 45-26, “O” for 25-6, and “U” for 5-0.
c) Find out closeness ranks.
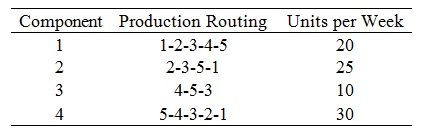
Question 4: What are the primary benefits of using computerized layout procedures versus Systematic Layout Planning (SLP) procedures done by hand?