Question 1: A fizzy drinks company makes five different flavours of drink on a single production line. The flavours are:
- Lemonade
- Cola
- Soda water
- Ginger Beer
- Dandelion & Burdock
The production line operates 5 days a week for 50 weeks a year. There are two weeks maintenance, which can be fitted in at the end of a convenient production cycle.
The annual sales, daily production rates, annual holding costs and ordering costs for the drinks are:
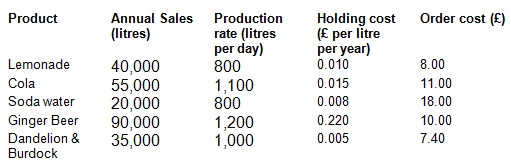
The drinks are produced in cycles. In each cycle, a batch of lemonade is produced, followed by a batch of cola and so on. The batch lengths (in days) for each drink are set simultaneously at the outset. Between each batch the equipment must be washed and cleaned, to avoid tainting of flavours. This does not take long but there is a cost, which depends on which the two drinks are. The costs of changing between drinks are:
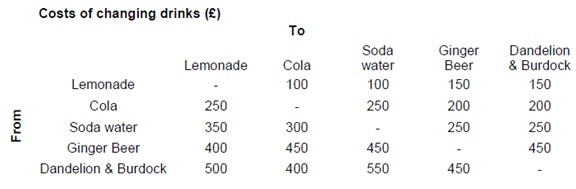
The company would like to know the answer to two questions:
1. In which order should the drinks be produced to minimise cleaning costs?
2. What is a practicable length for the production cycles and what should be the production of each drink be in those cycles, in order to minimise inventory costs?
Can you help?
Note that the optimum number of cycles per year (n) for a single item is (from the lecture notes):
In the case of many products, this becomes:
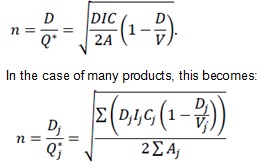
Note also that sales and production rates must be in the same units. You may find taking time of production easiest; thinking, for example, in terms of selling 5 days' production.