Problems:
Operational Optimization, Queueing, Linear Programming, Logistics, Flow Charts and Productivity
1. A company that makes shopping carts for supermarkets and other stores recently purchased some new equipment that reduces the labor content of the jobs needed to produce the shopping carts. Prior to buying the new equipment, the company used five workers, who produced an average of 80 carts per hour. Labor cost was $10/hour and machine cost was $40/hour. With the new equipment, it was possible to transfer one of the workers to another department, and equipment cost increased by $10/hour while output increased by four carts per hour.
a. Compute labor productivity under each system. Use carts per worker hour as the measure of labor productivity.
b. Compute the total productivity under each system. Use carts per dollar cost (labor plus equipment) as the measure.
c. Comment on the changes in productivity according to the two measures, and on which one you believe is the more pertinent in this situation?
3. The license renewal process at the State Automobile Driver's license office is designed as a service line, with customers processed in the fixed sequence listed in Table 1.
Task Description time/customer (seconds)
1 Review application for correctness 15
2 Process and record payment 30
3 Check for violations and restrictions 60
4 Conduct eye test 40
5 Photograph applicant 20
6 Issue license 30
Each task is performed by a separate clerk.
a. Draw a process flow diagram for the license renewal process.
b. What is the cycle time?
c. How many customers can the Office process in an hour.
d. Assuming that customers arrive at the Office at 60 second intervals, what is the throughput time?
e. How many customers will be in the Office, on the average, at any given time (once the system reaches a steady state) ?
f. The Office is under pressure to increase its productivity to accommodate 120 customers per hour with the addition of only one clerk to its present staff of six clerks. The manager of the Office observes that task 1, must be performed first and tasks 5 and 6 must be the last two steps, respectively. Tasks 2,3 and 4 can be performed in any sequence. Tasks can be combined with each other to create new (enlarged) tasks. (Note that it is OK to combine task 1 with another task as long as the employee who is assigned to this new task reviews application for correctness first and then performs the second part of the new task.) Design a system that will achieve the 120 customers/hour objective with the addition of one clerk. Provide a process flow diagram for the new system.
g. Compute the cycle time, capacity and throughput time for the system you designed in (f) above.
h. What is (are) the bottleneck(s) in the new system?
i. Will the system you designed in (f) above require additional expenditures in addition to the cost of the seventh clerk? Please be specific.
4. The following diagram describes how Dolphin Steel Co. makes steel.
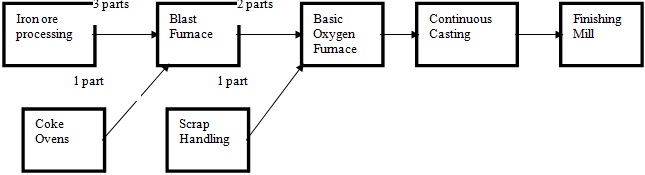
Stage Capacity ( tons/day)
Iron Ore Processing 4,000
Coke ovens 1,000
Blast furnace 3,000
Scrap handling 1,500
Basic Oxygen furnace 4,200
Continuous Casting 6,000
Finishing Mill 5,000
At two points in the steel making process, outputs from two departments are inputs to a single department. The ratio of each input is indicated on the arrow that illustrates the flow. For example, in the blast furnace, 3 tons of iron ore are mixed with 1 ton of coke.
a. What is the system capacity?
b. Which stage(s) in the process is a bottleneck?
c. How much can you increase the capacity of the system, by adding capacity to the bottleneck?
d. Assume that adding capacity requires a capital investment, say for example $2M. How would you go about determining if the investment is justified?
Now assume that the coke ovens, blast furnace and the basic oxygen furnace have yield rates of 80%, 85% and 90%, respectively. Please note that 80% yield means that for every 100 tons of input we get only 80 tons of output.
e. What is the system capacity?
f. Which stage(s) in the processes is (are) a bottleneck?