Discuss the below:
1. Good intermediate planning requires coordinating demand forecasts with _______________to determine feasibility and strategic fit.
2. The outcome of the 3-18 month S&OP is an _____________updated weekly/monthly balancing production quantities, timing and resources needed to meet demand at minimum cost.
3. Aggregate plan capacity options seek what?
4. Aggregate plan demand options seek what?
5. Using a level scheduling strategy to meet an 8,500 unit expected demand over 250 production days ___________units are made each day. At this output level, if it takes 2.3 hrs. to make a unit and a person works 8 hrs per day ___________workers are needed. If a worker is paid $15/hr. __________is the total labor cost?
6. In your factory you decide to follow a level labor strategy. 23 pieces are made per day. What is the inventory at the end of Feb__________? The total inventory carried over from one month to the next from Jan to April is ____________units. With inventory carrying cost @ $2/unit per month, total carrying cost is_______________units.
7. To reduce inventory costs your production dept. would like to consider using part-time labor & subcontracting. The output chosen is no longer 23; output chosen is to meet the month of lowest demand. What is that output level (using the table in question 6)?
8. When producing this level of units/day over 80 production days, a total of __________units are made in-house. If it takes 0.9 hrs to make each unit and workers work 7 hrs per day, how many full and part-time workers are needed______________? To meet the 1840 units demanded ___________will be outsourced.
9. You are making a very simple product. Your HR manager recommends hiring & laying off full-time & part time people to meet monthly demand. It takes 2 hrs to make a unit and workers work 7 hrs per day. How many workers are needed each month?
|
Expected demand per production day
|
Jan
|
12
|
Feb
|
25
|
Mar
|
25
|
April
|
18
|
10. If it costs $200 to hire a worker and $400 to lay off a worker, how much is spent in total on hiring and laying off Jan through April?
11. From the aggregate S&OP plan we know in broad terms what needs to be made. The ______________breaks down (i.e. disaggregates) the plan into specific products to be made by when.
12. In this Bill of Material (BOM) we have _______ levels. Circle the parent items in the BOM.
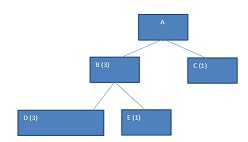
13. In the above BOM, to make 100 items of A, how many of items B,C,D and E must be made?
14.What is subtracted from a gross requirement plan to give you the net requirement plan?
15. In the below plan, your EOQ is 100 pieces. What is the net requirement in week 5?
|
Week 1
|
Week 2
|
Week 3
|
Week 4
|
Week 5
|
|
|
|
|
|
|
Gross Requirements
|
60
|
40
|
10
|
20
|
40
|
Projected on hand
|
20
|
0
|
|
|
|
Net requirements
|
40
|
40
|
|
|
?
|
Planned order receipt
|
|
100
|
|
|
|
Planned order release
|
100
|
|
|
|
100
|
16. As a manufacturing strategy, matching demand is best when set up costs are ________and holding costs __________. EOQ is effective when demand is ____________.