Bearing stresses are very common in aerospace engineering. It occurs on the surface of contact between any two structural members. Bolts, pins, and rivets are classic examples of where bearing stresses occur. You will find these in many flight vehicles.
A simplified example of this is a bolt pressed against the flat surface of a bar. This might occur during flexure testing of a material. The stresses in an elastic material under a concentrated line load P (units of [Force/Length]) are given by the following equations
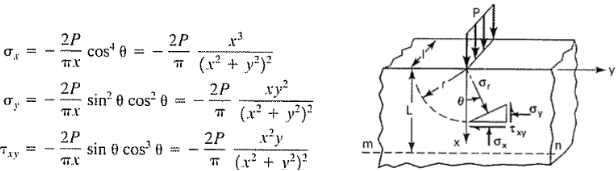
Using non-dimensional coordinates (x' = x/a, y' = y/a ):
a) Make a three-dimensional surface plot and a two-dimensional (non-flooded) contour line plot of the absolute maximum non-dimensional shear stress [Τ/[P/a]) as a two dimensional function of x and y. Use the ranges:0 ≤ x ≤ 3; -2 ≤ y ≤ 2
b) Comment on your results. (Don't just summarize the steps you followed. Considering the results, discuss what the final results tell you, whether they have any interesting features, etc.)
Values for P and a are not required. Your Mechanics of Materials textbook provides you with the equations needed to calculate the principle stresses. Your plots must make use of good plotting practices (scaling, labels, legend, etc.). You must write a MATLAB script, saved in a .m file. The script should include the commands to complete the calculations and to create your plots in multiple windows.